Las herramientas prácticas o métodos de Lean Manufacturing que establecen los cimientos lean son las que apoyan la búsqueda de estabilidad del sistema productivo. Más específicamente, estos cimientos lean son nivelación, estandarización y Kaizen.
¿Qué herramientas nos permiten alcanzar y mantener la estabilidad del sistema productivo?
De un lado, aquellas herramientas que facilitan la construcción y mantenimiento de los cimientos lean, asociadas al “management o gestión de lo cotidiano”. De otro, el mantenimiento productivo total (TPM). Las primeras son, entre otras, las 5 S, Gestión Visual, Estandarización del trabajo o Kaizen. En este sentido, el “management de lo cotidiano” es la gestión de aquellas actividades realizadas en el día a día de una empresa. Estas herramientas suelen resultar de fácil aplicación. Generalmente la implantación de éstas, representan el punto de partida para asentar los cimientos Lean. A continuación, incluimos las herramientas más ampliamente extendidas que sostienen los fundamentos base o cimientos de un sistema Lean.
¿Cuáles son las llamadas 5S?
Esta es una de las herramientas más ampliamente utilizadas en la “construcción” de los cimientos lean. La cultura japonesa es conocida por su disciplina, respeto por el orden y jerarquía. Todo ello perfectamente integrado en su hacer cotidiano. Toyota trasladó esta forma de vida al ámbito empresarial mediante la técnica o metodología de las 5S, en los 60. La incorporó como un aspecto clave en lo que serían los cimientos lean de su casa Toyota. Las 5S es un método de organización del puesto de trabajo, es decir, mantenerlo despejado, organizado y limpio. ¿Qué significan, por tanto, cada una de las 5 S, en el contexto de “construir” los cimientos lean de una empresa?
- SEIRI (despejar). Recorrer el lugar de trabajo, distinguir y separar lo necesario de lo innecesario. Se dispone de un área de descarte y determina el destino de lo innecesario: eliminación, venta, donación, etc.
- SEITON (ordenar). Definir un lugar para cada cosa y colocar cada cosa en su lugar. Se señaliza perfectamente la ubicación de acuerdo a su uso e identifica los elementos que en ella ubiquemos.
- SEISO (limpiar). Limpiar, mantener limpio y no volver a ensuciar. Se planifica la limpieza de cada elemento y de cada sector o zona.
- SEIKETSU (estandarizar). Definir los estados de referencia y estandarizar, creando normas sencillas y visibles para todos.
- SHITSUKE (disciplina). Seguir mejorando.
Los beneficios de su implantación en el desarrollo de los cimientos lean de una empresa son múltiples, por citar algunos:
- Reducción de esperas.
- Movimientos o transportes.
- Incremento de la seguridad de los trabajadores.
- Aumento de la motivación del personal debido a un entorno de trabajo más agradable.
- Mejora de la imagen de la empresa.
¿En qué consiste la gestión o control visual?
En primer lugar, esta herramienta está muy ligada a la anterior y también resulta clave en la “construcción” de los cimientos Lean. Consiste en un conjunto de controles, que permiten la gestión sencilla y visual de la situación del sistema productivo. En consecuencia, cualquier error cotidiano, es perfectamente visible, permitiendo detectar problemas en fase inicial. Además, el diseño e implantación de la gestión visual de una empresa es muy particular y diversa. Por lo general, hay multitud de herramientas y/o técnicas diferentes que se utilizan para aplicar la administración visual en el lugar de trabajo. Las herramientas más simples y ampliamente extendidas son:
- Identificación de ubicaciones mediante etiquetado.
- Señales de seguridad estandarizadas.
- Tableros de herramienta con cuadros de sombras.
- Láminas translúcidas de colores para marcación de rangos de utilización de medidores.
Tambien se puede resaltar que existen otras más complejas cómo Andon. En todo caso, en la “construcción” de sus cimientos Lean, cada empresa elegirá la opción que mejor encaje con su actividad. En cuanto a sus beneficios, tendremos la mejora del flujo de información relevante y la estandarización de la comunicación. Además, enriquece la relación entre áreas o departamentos y reduce el tiempo de respuesta.
¿Es necesaria la estandarización dentro de la filosofía Lean?
Taiichi Ohno sostenía lo siguiente: “si no hay estandarización, no es posible la mejora”. La estandarización constituye una necesidad básica en el aseguramiento de los cimientos Lean de una empresa. Permite controlar la productividad, la calidad y la seguridad del proceso en su conjunto. Además, garantiza que las actividades requeridas se realicen en los plazos establecidos y con un inventario definido. Un estándar es la descripción escrita y/o gráfica que ayuda a un trabajador en el ejercicio cotidiano de su actividad. Por ejemplo, comprender el funcionamiento de una máquina, una técnica, etc. Todo ello con la intención de hacer productos de calidad con la mayor fiabilidad y seguridad posible. Existen multitud de los modelos o herramientas de estandarización. Algunas de las más utilizadas son:
- Hojas de recopilación de datos.
- Verificación o chequeo.
- Procedimientos operacionales y de carácter general (instrucciones de trabajo).
- Guías técnicas.
- Diagramas (flujo, funcionales, etc.).
¿Qué significa KAIZEN?
Kaizen se define a partir de dos palabras japonesas, “KAI” que significa cambio y “ZEN”, mejora. Por tanto, Kaizen es “cambio a mejor”. Esta herramienta integral de los cimientos Lean está especialmente dirigida a los empleados. Además, básicamente es una herramienta basada en pequeñas mejoras llevadas a cabo como resultado de distintos esfuerzos progresivos. Otro aspecto a destacar es que un evento Kaizen puede ser:
- Formal (supone organización de la actividad de mejora propuesta).
- Informal (supone creatividad o simple sentido común, tiene carácter inmediato y no implica costes de inversión).
La filosofía Kaizen
También se habla de 10 mandamientos Kaizen, conceptos integrales de esta herramienta:
- Abrir la mente a posibles cambios.
- Se puede hacer si se conoce como hacerlo.
- No se debe atacar a las personas sino a los problemas o procesos ineficientes.
- Buscar soluciones simples.
- Si algo falla, detenerse hasta encontrar el origen del problema y solucionarlo.
- Utilizar la creatividad y/o el sentido común frente a la inversión económica.
- Los problemas son oportunidades disfrazadas.
- Buscar la causa real, preguntarse por qué una y otra vez, hasta llegar a la solución.
- Trabajar en equipo, no buscar el reconocimiento propio por encima de todo.
- La mejora continua no tiene límite, pues es infinita.
Por otro lado, la correcta aplicación de la filosofía Kaizen es una parte fundamental de los cimientos Lean. Como resultado, se apoya, como mínimo, en 4 principios fundamentales:
- Optimización de los recursos de los que se dispone.
- Implementación rápida de las soluciones encontradas.
- Bajo o nulo coste.
- Participación activa del operario.
En general, la estrategia Kaizen suele desarrollarse de forma combinada con la innovación y su implantación resulta muy sencilla. Sobre los cimientos Lean, se identifica una oportunidad de mejora, se planifica y aplica. Se revisa y tras cumplimiento de lo establecido inicialmente, se estandariza.
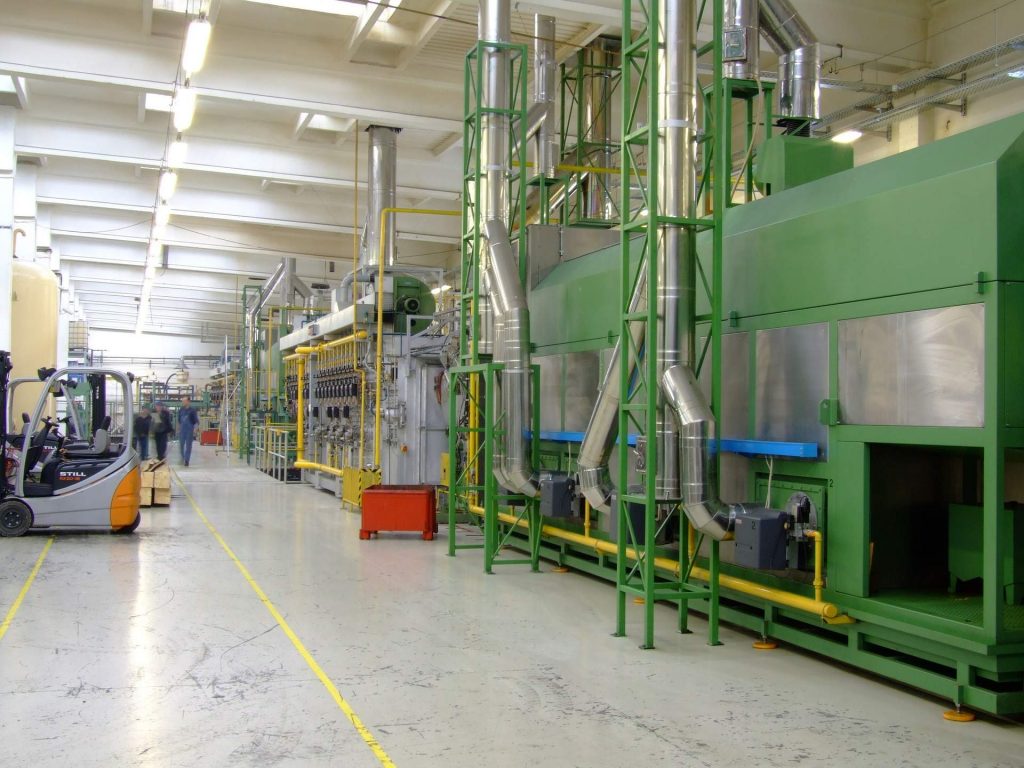
¿Qué es el TPM?
En primer lugar, esta herramienta está relacionada íntimamente con las 5 S y por ende, con la “construcción” de los cimientos Lean. Por tanto, TPM es el acrónimo de Total Productive Maintenance, Mantenimiento Productivo Total en castellano. Se trata de una metodología de mantenimiento de equipos de trabajo y plantas de fabricación. De forma general, persigue 4 objetivos básicos, con el fin de construir y mantener unos cimientos Lean sólidos. Éstos son cero accidentes, cero paradas, cero defectos y cero desperdicios. Por su parte, sus principios fundamentales son:
- La participación de todo el personal en las actividades cotidianas.
- Una cultura corporativa dirigida a establecer los cimientos de la máxima eficacia productiva y de gestión de equipos.
- La implantación de un sistema de gestión de la producción tal que se eviten pérdidas, anticipándose a las mismas.
- La implementación del mantenimiento preventivo como pilar básico de la actividad productiva.
- Y la aplicación de los sistemas de gestión de todos los aspectos productivos, incluyendo diseño, desarrollo, ventas y dirección.
Además esta filosofía considera que existen 6 grandes pérdidas para la empresa:
- Averías.
- Preparación y ajustes.
- Paradas menores y tiempos muertos.
- Velocidad de operación reducida.
- Defectos.
- Arranque.
Los 8 pilares TPM
Cabe destacar que los pilares de la misma suelen representarse mediante un templo, siendo los cimientos Lean del mismo las 5 S. Y, sobre ésta, los 8 pilares TPM:
- Mantenimiento autónomo.
- Mejora enfocada.
- Mantenimiento planificado.
- Mantenimiento de calidad.
- Prevención del mantenimiento.
- Formación.
- TPM en tareas administrativas.
- Seguridad y Medioambiente.
Por otro lado, los beneficios de su implantación como apoyo en la “construcción” y mantenimiento de los cimientos Lean, entre otros, serán:
- Eliminación de las pérdidas asociadas al mantenimiento incorrecto.
- Mejora de la fiabilidad.
- Disponibilidad de los equipos o la reducción de los costes de mantenimiento.